Plasmas for Deposition
Plasmas do some really neat stuff for the CVD engineer -- and they also have some really nasty features you have to be aware of.
Virtues
Consider a typical capacitive plasma. The electron temperature might be 3 eV; the ion and neutral temperatures are much smaller. As shown in the table below, the number of electrons with sufficient energy to dissociate a molecule is 10 to 100 times larger than the number that can ionize; the plasma will produce a large supply of excited and dissociated molecules and thus reactive radicals, even for a modest fractional ionization.
Substance
DissociationEnergy (eV)
IonizationEnergy (eV)
n(diss)/n(ion)@ Te=3 V
H2
4.5
15.4
38
O2
5.2
12
9.6
CH4
4.5
12.6
15
F2
1.6
15.7
109
Thus the first reason to use a plasma is to crack relatively stable molecules apart, thus encouraging deposition, at much lower temperatures than would otherwise be possible, as shown for some common films in the table below.
Film
Precursors
ThermalDeposition
PlasmaEnhanced
silicon nitride
SiH4or SiH2Cl2 and NH3
750°C
200-500°C silicon dioxide
SiH4 and O2 or N2O
350-550°C 200-400°C
TEOS and O2 700-900°C 300-500°C amorphous silicon
1.6
550-650°C 200-400°C
TEOS = tetraethyl orthosilicate, Si(OC2H5)4
The second reason to use plasma deposition is more subtle but of great importance. Recall that surfaces exposed to a capacitive plasma are subject to bombardment by energetic ions, whose kinetic energy can vary from a few eV to 100's of electron volts. Ion bombardment of this nature has very significant effects on the properties of the deposited film. Increasing ion bombardment tends to make films denser and cause the film stress to become more compressive.
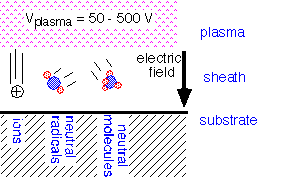
The densification effects arise from the collision cascade which is induced when a high-energy ion strikes the surface: any "holes" under the surface atoms tend to get filled in.
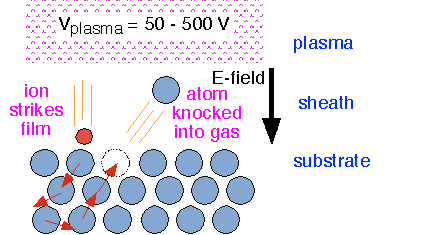
It is often the case than dielectric films that are porous and under tensile stress cause reliability problems in IC fabrication. Plasma-enhanced deposition techniques can deposit dense films at temperatures hundreds of degrees less than required for thermal densification. However, excessive compressive stress can also lead to impaired reliability. The ability to adjust stress, through changes in process conditions, chamber geometry, or excitation (dual frequency mixtures) is of considerable importance in successful semiconductor processing.
As we will consider in more detail in discussing sheath ion flux and the Bohm velocity, typical values of bombardment flux are 0.002 to 0.2 monolayers/second. The ratio of ion flux to growth flux determines what effect bombardment has on the properties of the growing film. High density plasma reactors are required to achieve ion fluxes greater than growth rates.
A final important benefit of plasma deposition is the ability to easily clean the reactor. For example, by introducing a fluorine-containing gas (e.g. CF4) and igniting a plasma, one can clean silicon, silicon nitride, or (with rather more difficulty) silicon dioxide from the electrodes and chamber walls. Chamber cleaning is of great practical importance; thick films built up on the parts of a chamber may "spall" (break off), creating particles which can fall onto the substrates and cause defects in circuit patterns, reducing the yield of good circuits from the process.
...and Vices
The bombardment of surfaces with ions also leads to sputtering: the displacement of atoms from the surface into the gas phase by incoming ions. The displaced ions diffuse through the gas and can land anywhere in the chamber, including on the substrates. Sputtering can be an important source of trace metallic contamination in PECVD films.
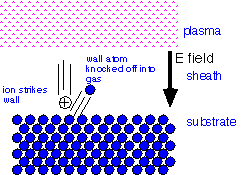
Sputtering of substrate material can be intentionally exploited to improve the conformality and gap filling ability of deposited films: this is typically done using high-density plasma reactors, and will be discussed in more detailed in the section on reactor designs. Ion bombardment is different on horizontal and vertical surfaces; thus, the composition and density of films can depend on the topography.
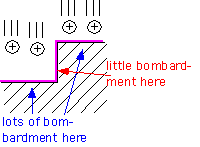
Plasma deposition of metallic or other highly conductive films is challenging: the deposited film tends to short out the powered electrode of a capacitive plasma reactor, or coat the dielectric window of an inductive reactor, shielding the chamber from the magnetic field.
The plasma generation apparatus adds considerably to the complexity and cost of reactors, and complicates operation. The plasma requires one or more power supplies, each with an appropriate matching network, and electrically insulating but mechanically sound materials for isolating powered electrodes. Substrate heaters must be electrically isolated from the plasma. Choice of materials is influenced by the possibility of contamination.
The Role of Transport in Plasma-Enhanced CVD
- Gas phase chemistry: Species formation is strongly influenced by residence time, pressure; the neutral gas temperature is rather irrelevant
- Temperature control: Heat transport is not much affected by the presence of a plasma, but the plasma represents an extra source of heat: tens to as many as thousands of Watts, typically dissipated on all surfaces exposed to the plasma. If most of the bias voltage is on one electrode (e.g. a small-area-ratio reactor or a high-density reactor), a great deal of power will be dissipated there due to ion bombardment. This is often dumped onto the wafer, and must be removed using e.g. backside gas injection.
- Uniformity: Control of plasma uniformity and plasma chemistry dominate film deposition rate; the transport parameters are second-order effects except when depletion is significant.
- Plasma Collisions: Higher pressures give more loss of energy from electrons to neutrals, but more plasma confinement due to reduced electron diffusivity.
Return to Tutorial Table of Contents
Book version of the CVD Tutorial